The
first
mushroom
casket
burial
in
the
U.S.
took
place
for
Mark
C.
Ancker
in
Industry,
Maine
on
June
1,
2025.
Loop
Biotech
Why
you
can
trust
us
Founded
in
2005
as
an
Ohio-based
environmental
newspaper,
EcoWatch
is
a
digital
platform
dedicated
to
publishing
quality,
science-based
content
on
environmental
issues,
causes,
and
solutions.
With
all
the
chemicals,
wood
and
land
used
in
traditional
burials,
they
can
be
detrimental
to
the
environment.
Now,
a
company
from
the
Netherlands
has
developed
a
casket
made
entirely
of
mycelium
—
the
network
of
thread-like
structures
that
make
up
mushroom
roots
—
that
biodegrades
within
45
days
of
burial.
The
innovative
Loop
Living
Cocoon
mushroom
casket
is
grown
in
one
week
and
enriches
the
soil
while
nourishing
new
plant
life.
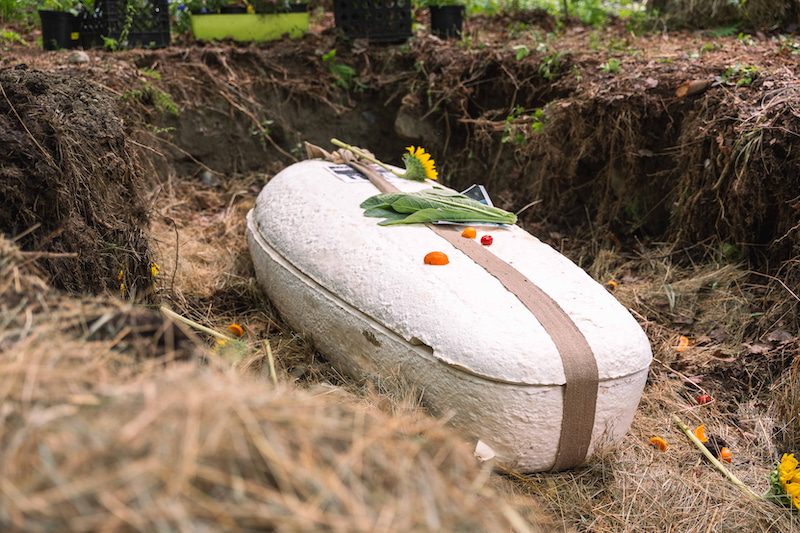
Loop
Biotech
Recently
the
first
burial
using
a
mushroom
casket
took
place
in
North
America,
on
a
peaceful
hillside
in
rural
Maine,
a
press
release
from
Loop
Biotech
said.
“My
father
always
told
me
that
he
wanted
to
be
buried
in
the
woods
on
the
property
that
he
loved
so
much,”
said
Marsya
Ancker,
who
chose
a
mushroom
casket
for
the
burial
of
her
father
Mark
C.
Ancker.
“He
wanted
his
final
resting
place
to
nourish
the
land
and
plants
he
cherished.”
Since
2021,
Netherlands-based
Loop
Biotech
has
facilitated
more
than
2,500
burials
using
mushroom
caskets
all
over
Europe,
but
the
service
in
Maine
was
a
first
for
North
America.
“Green
burial,
which
gained
renewed
attention
in
the
1990s,
replaces
traditional
embalming
chemicals,
hardwood
caskets,
and
synthetic
linings
with
biodegradable
materials
that
enable
natural
decomposition,”
Loop
Biotech
said
in
the
press
release.
Founded
in
2005,
the
nonprofit
Green
Burial
Council
has
seen
marked
growth
in
green
burials,
documenting
a
72
percent
increase
in
cemeteries
seeking
sustainable
end-of-life
options.
“Since
2005,
the
Green
Burial
Council
has
certified
over
250
providers
and
recorded
400+
green
cemeteries
across
the
U.S.
and
Canada:
a
clear
sign
of
growing
demand
for
environmentally
conscious
end-of-life
choices,”
said
Sam
Perry,
president
of
the
Green
Burial
Council.
“More
and
more
people
are
seeking
meaningful
alternatives
that
honor
both
their
loved
ones
and
the
planet.”
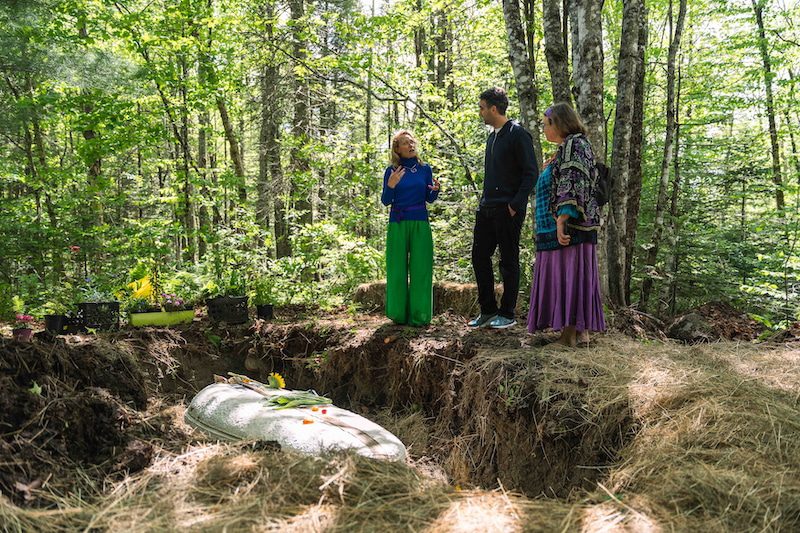
Loop
Biotech
According
to
the
Green
Burial
Council,
conventional
burials
in
the
United
States
use
approximately
20
million
board
feet
of
wood,
4.3
million
gallons
of
embalming
fluid
and
1.6
million
tons
of
concrete
reinforced
with
steel
each
year.
The
Global
Green
Burial
Alliance
was
founded
in
2022
and
is
an
entirely
free,
volunteer-run
networking
organization.
It
creates
educational
opportunities
while
connecting
consumers
with
providers
and
encouraging
families
to
reclaim
their
voice
in
how
their
loved
ones
are
laid
to
rest.
“Funerals
can
be
more
than
endings:
they
can
be
beginnings,”
said
Bob
Hendrikx,
Loop
Biotech’s
founder.
“We
created
the
Loop
Living
CocoonTM
to
offer
a
way
for
humans
to
enrich
nature
after
death.
It’s
about
leaving
the
world
better
than
we
found
it.”
Loop
Biotech
is
part
of
a
rising
tide
of
innovations
intended
to
reimagine
the
burial
process
while
reversing
the
environmental
harm
of
the
funeral
industry.
The
Ancker
Family
conducted
their
service
on
private
land
located
in
Industry,
Maine.
While
they
kept
the
ceremony
small,
they
hope
that
by
sharing
their
story
it
might
be
an
inspiration
to
others
contemplating
ways
of
saying
goodbye
that
are
more
conscious
and
Earth-friendly.
“Death
is
the
only
guarantee
in
life;
it
is
how
we
choose
to
embrace
death
that
paints
the
landscape
for
generations
to
come.
To
embrace
the
living
with
our
death
becomes
the
final
act
of
kindness
we
can
bestow
upon
our
planet,”
said
Ed
Bixby,
founder
of
Global
Green
Burial
Alliance.
Subscribe
to
get
exclusive
updates
in
our
daily
newsletter!
By
signing
up,
you
agree
to
the
Terms
of
Use and Privacy
Policy,
and
to
receive
electronic
communications
from
EcoWatch
Media
Group,
which
may
include
marketing
promotions,
advertisements
and
sponsored
content.